Maiden Electron Launch Cut Short by Faulty Ground Equipment

Launch Services Provider Rocket Lab on Monday shared details on why the inaugural launch of the company’s Electron rocket failed to reach orbit, concluding that a faulty piece of ground telemetry equipment was responsible for the flight’s untimely end as opposed to a problem with the launch vehicle.
The inaugural Electron flight – nicknamed ‘It’s a Test’ – blasted off from Rocket Lab’s launch pad on Mahia Peninsula, New Zealand on May 25 after several days of delays. Powering away from New Zealand’s North Island, the 17-meter tall Electron fired its nine electric pump-fed first stage engines to climb into space – a novelty in rocketry. First stage flight went as expected and Electron successfully fired up its single-engine second stage, but in the end could not reach orbit.
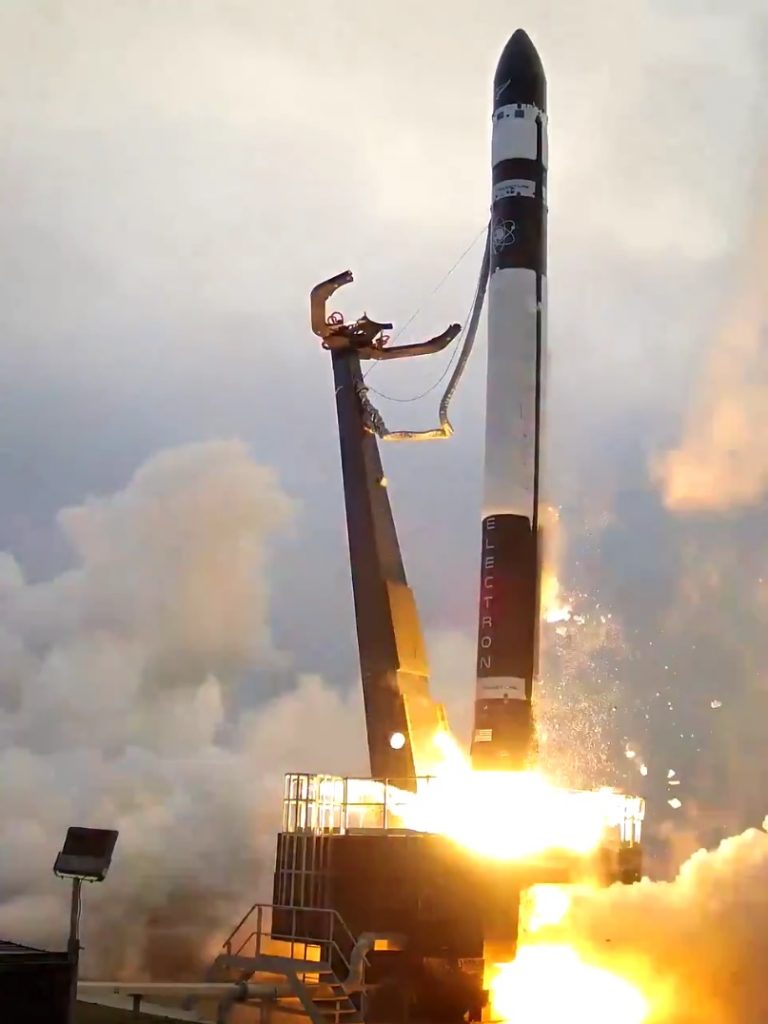
Although the mission did not achieve orbit while intending to do so, ‘It’s a Test’ was counted as an overall success for Rocket Lab – demonstrating the design of the Electron first stage and collecting invaluable data needed for ironing out any deficiencies for the next test flight. Rocket Lab did not immediately share the cause of Electron’s failure to reach orbit, but emphasized the flight’s significant achievement of reaching space and demonstrating all of Electron’s components, including critical stage and payload fairing separation events.
After the mission, Rocket Lab engineering teams combed through over 25,000 channels of data collected during the flight to understand what caused the rocket to fall short of orbit and provide a detailed assessment on how all launch vehicle subsystems performed in the actual flight environment. “The review found the launch had to be terminated due to an independent contractor’s ground equipment issue, rather than an issue with the rocket,” the company said in a statement. “Rocket Lab’s investigation board has identified the root causes and corrective actions.”
According to Rocket Lab’s post-mortem analysis, Electron had climbed to an altitude of 224 Kilometers when, around four minutes into the flight, ground telemetry equipment operated at the Mahia launch site by a third-party contractor lost contact with the launch vehicle. Per standard procedure, range safety officials made the call to terminate the flight and issued the destruct commands to the rocket’s Flight Termination System. Data from Rocket Lab’s own telemetry equipment confirmed the rocket was following a nominal trajectory and was performing as planned at the time of flight termination.

As part of its investigation, Rocket Lab found that the telemetry chain in question did not have forward error correction enabled which led to corrupt position data being processed by the range safety receiving chain, resulting in the untimely end of the mission. Forward error correction (FEC) is a commonly used technique for controlling errors in data transmission over potentially noisy communication channels.
Typically, FEC is implemented by a sender encoding its messages in a redundant way using an error-correcting code with parity bits. At the receiving end, the signal is decoded and a limited number of errors in the received message can be corrected via the parity bits. FEC allows the receiver to correct errors without the need for a forward channel to request re-transmission of data (which does not exits for launch vehicles).
In Electron’s case, FEC on the contractor equipment was disabled, meaning the system was outputting the received data without any decoding or error correction. In the initial minutes of flight (with the vehicle close to the launch site), the signal-to-noise ratio within the received radio signal was high and no errors occurred as clean data was received. As the rocket accelerated downrange, distance between the sender and receiver grew and with that increased the noise within the radio signals, causing the error rate to increase to a point where positioning data from the vehicle was scrambled long enough to violate range safety criteria.
In essence, Electron’s flight was cut short because a switch was flipped incorrectly and FEC was turned off, eliminating the ground system’s ability to correct the noisy radio signal as the rocket moved away from the receiver at the launch site.
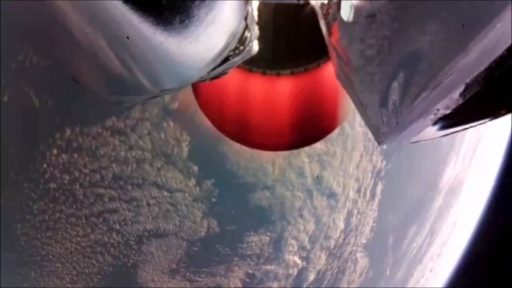
Rocket Lab’s own telemetry equipment – operated at the correct settings – did not suffer similar data loss and the company also demonstrated via replaying of raw radio data recorded during launch that a correctly configured system on the contractor side would also resolve the problem.
“The fix for the issue is simple and corrective procedures have been put in place to prevent a similar issue in future,” Rocket Lab said and also noted that no major changes to the Electron launch vehicle hardware have been required after combing through data from the inaugural launch. Another issue addressed by Rocket Lab was the rolling motion evident throughout first stage flight with some corrective action needed via parameter adjustments to reduce or eliminate the inadvertent roll for the next test flight.
Going forward, Rocket Lab is preparing for its second Electron test flight that will be aptly named ‘Still Testing.’ The launch vehicle for the mission has been integrated and is preparing for shipment to the Mahia launch site with rollout to the launch pad planned in around eight weeks time, placing ‘Still Testing’ no earlier than October. The focus for the second flight will be on achieving orbit as Flight #1 has demonstrated all critical flight events up to stable operation of the rocket’s second stage, building confidence in Electron’s overall design and Rocket Lab’s plan of starting commercial operations after three test flights.

Electron is sized for the growing-small satellite market, capable of launching satellites of up to 150 Kilograms in single-payload deliveries and lifting clusters of CubeSats. Rocket Lab plans to charge $4.9 million per Electron flight, significantly less than any other launch services provider currently in operation.
Electron, sometimes called the ‘first battery-powered’ rocket, is the first orbital launch vehicle to rely on electric-pump-fed engines, 3D printing for all major engine components and an all-carbon-composite structure – creating a 21st century launch vehicle. Standing 17 meters tall, Electron measures 1.2 meters in diameter and weighs in at 12,550 Kilograms when fully loaded with Liquid Oxygen oxidizer and Kerosene fuel – a common and well-understood propellant combination. One of Rocket Lab’s flagship developments is the Rutherford engine, the first electric pump-fed engine to reach the launch pad, substituting complex turbomachinery driven by high-pressure combustion gases with a pair of brushless electric motors that drive the engine’s fuel and oxidizer pumps.